Multiquip® Finds Steady Solution in Vanguard® 200 Engine
In today’s fast-paced world, there isn’t much time or tolerance for bumps or disruptions. That expectation is no different in the construction industry — especially when it comes to laying smooth, even concrete.
Founded in 1973, Multiquip is one of the largest, most diversified manufacturers and suppliers of world-class quality products and solutions for the construction and industrial markets. When Multiquip needed a new power solution for its J36B65 walk-behind trowel product, the engineers at Briggs & Stratton knew they had just the commercial engine for the job.
“We were facing a number of challenges with our previous engine supplier for the walk-behind trowel, so we went looking for a solution that would fit the current footprint and reduce vibration and noise levels,” says Jordan Carmean, designer at Multiquip.
Pickin’ up good vibrations
After testing a few options, the product managers at Multiquip felt like they had found an engine with superior vibration characteristics in the Vanguard 200 single-cylinder engine.
“A big issue with walk-behind trowels in particular is that you can get a lot of vibration off the engine,” says Dylan Rewoldt, manager sales, constructional industrial categories at Briggs & Stratton. “That vibration can affect the concrete pour because you’re not going to get as smooth of a surface in the final product.”
Air filtration was another area where Vanguard won out over the previous engine. Concrete work is particularly dusty, and the Integrated Cyclonic Air Filtration System from Vanguard helps the engine perform consistently even under harsh conditions.
“Ultimately, we went with Vanguard because of its robust power, name recognition and reliability,” said Carmean.
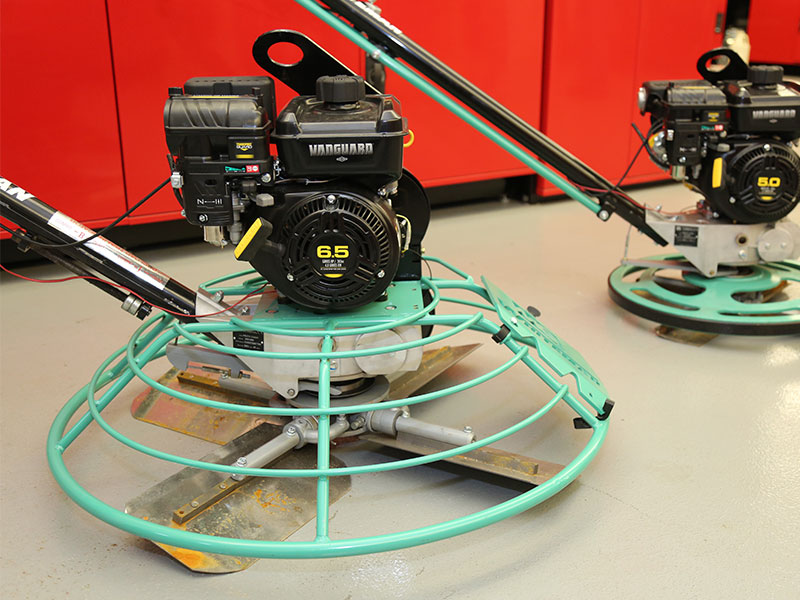
Put to the test
While the Multiquip team could feel the difference in vibration when testing the Vanguard engine in its walk-behind trowel, there was a way to quantify and prove the difference — the Briggs & Stratton Power Application Center (PAC).
The PAC offers manufacturers the opportunity to put equipment through rigorous testing to ensure it can withstand the tough environments it will face in the field. At the PAC, trained application engineers test equipment in scenarios like extreme heat and sub-zero temperatures. They also work to address noise and vibration elements that may impact productivity and operator comfort.
“At the PAC, we do a lot of testing for our customers to ensure a power solution is a good fit for a particular product,” said Chris Krajewski, PE, application engineer at Briggs & Stratton. “Our goal is to provide application-related support by analyzing, evaluating and improving product design to ensure our customers are successful.”
The PAC will go to great lengths to do thorough testing. In the case of testing products like a walk-behind trowel, the PAC team made sure they had the right environment to simulate the conditions the machine would face on the job.
“Sometimes, we have to be a little creative in how we test the equipment,” says Krajewski “For the trowels, we actually got a slab of concrete poured at the PAC to create an actual test pad. We do everything we can to try and replicate what they're testing and what it's like in the field.”
Testing support — near or far
Since the pandemic has significantly disrupted work environments, the PAC has become skilled at working with their customers from afar and sharing progress virtually.
“I didn’t spend any time at the PAC in person,” says Carmean. “Even so, it was extremely straightforward and simple getting the machines to the PAC and back. It was really painless, to be honest.”
Virtual connection is becoming the norm at the PAC, and the experts there are taking this change in stride.
“I'd say most of our customers are out of state, and it’s hard for us to visit them or for them to visit us,” says Krajewski. “Especially with this pandemic, everyone's becoming familiar and comfortable with doing video calls. If we need to jump on a call or if they need to show me something on video chat, we can do that. We stay pretty flexible”
The results
After testing the walk-behind trowel with the Vanguard engine, the PAC saw a 20 percent reduction in vibration levels compared to what Multiquip had with its previous engine. Both the Vanguard and Multiquip teams noticed a significant reduction in noise levels, as well.
“The tone of the Vanguard engine just seems, I don't know how else to put it, much less obnoxious,” says Carmean. “That’s something I know operators will appreciate since they are working with these machines all day long.”
That “less obnoxious” sound can be attributed to the acoustically designed Vanguard engine. The engine’s air cleaner, fuel tank and muffler are all optimized to reduce noise and deliver improved tonal quality."
The team at the PAC was also able to complete the testing process two weeks ahead of schedule, which helped Multiquip evaluate the engine and make a power solution decision quicker than expected.
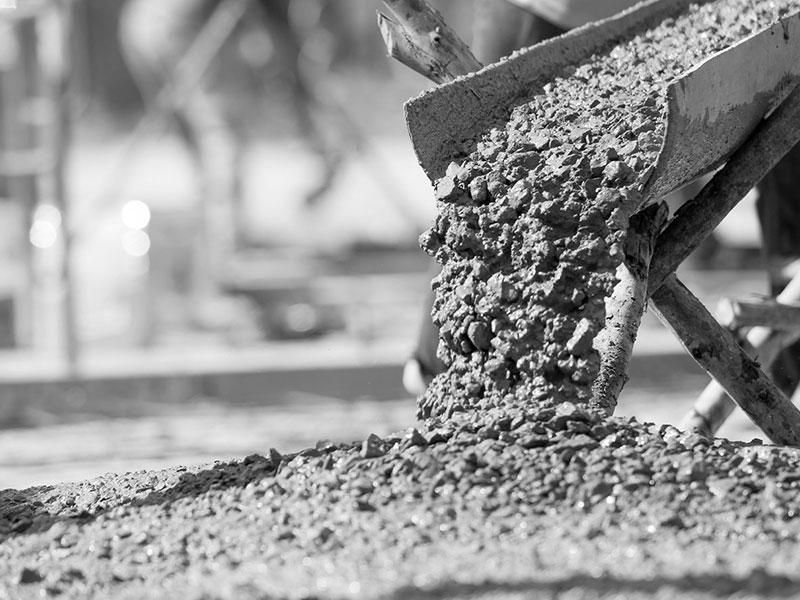
Paving a smooth road for future partnerships
In an industry that can bring a lot of ups and downs, the Multiquip team was grateful to have such a steady, attentive partner in Vanguard.
“Vanguard really emphasises the follow-through,” says Carmean. “As simple as that sounds, they are just so quick to answer the questions, answer the emails, and return the phone calls. Then, they nailed the turnaround with testing and returning the units to us in a very timely manner. I’m very impressed because, at other places, your emails go unread for long periods of time and projects seem to drag out. That wasn’t the case here at all.”
Looking ahead, the Briggs & Stratton team is looking forward to continuing to be a partner and power provider to Multiquip as the company navigates the evolving needs of its customers and stakeholders. What’s coming next for the two companies is sure to be interesting — maybe even electrifying. Stay tuned.
Find out what it's like to work with Vanguard here.
About Briggs & Stratton:
Briggs & Stratton, headquartered in Milwaukee, Wisconsin, provides innovative products and diverse power solutions to help people get work done. Briggs & Stratton is the world’s largest producer of engines for outdoor power equipment, and is a leading designer, manufacturer and marketer of lithium-ion battery, standby generator, energy storage system, lawn and garden, turf care and job site products through its Briggs & Stratton®, Vanguard®, Ferris®, Simplicity®, Snapper®, Billy Goat®, Allmand®, SimpliPhi®, Branco® and Victa® brands. Briggs & Stratton products are designed, manufactured, marketed and serviced in more than 100 countries on six continents. For additional information, please visit www.basco.com and www.briggsandstratton.com.