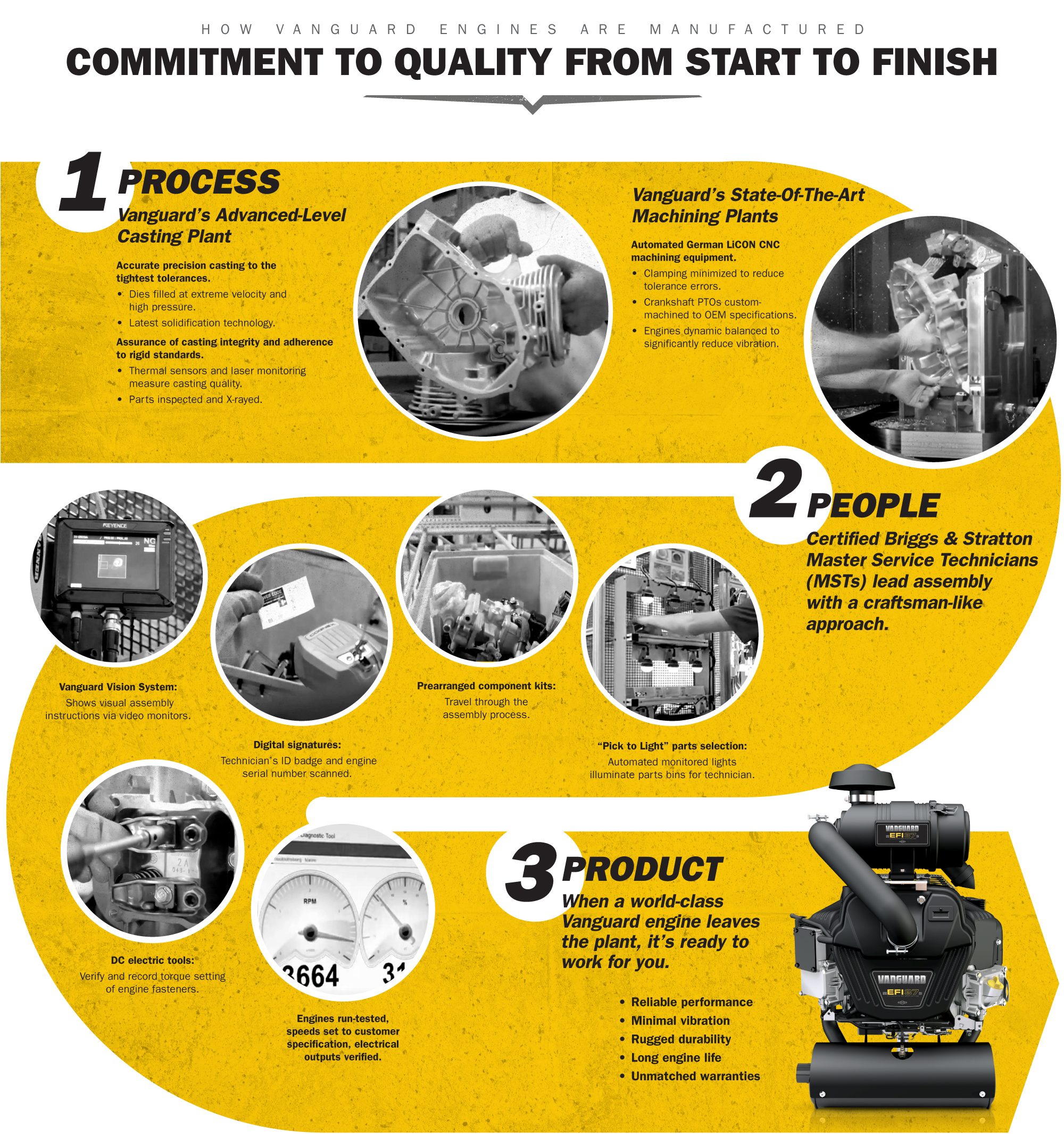
HOW VANGUARD V-TWIN ENGINES ARE MADE
The unique Vanguard Manufacturing System demonstrates our personal commitment to quality from start to finish. Each part of our manufacturing process is designed for extreme precision, accuracy and quality control. We call it the 3 Ps. And it’s why construction equipment manufacturers can be confident that Vanguard engines deliver the rugged reliability and exceptional performance they expect from our brand.
PROCESS
Vanguard engine parts are made at our own advanced-level casting plant using the very latest precision casting technology. Using extreme velocity and high pressure, only inspected metal from certified suppliers is used to fill dies to the tightest tolerances and the latest solidification technology is built into each die. At every step of the casting process, we take quality control to the extreme. Casting quality is measured at predetermined points using thermal sensors and laser monitoring, along with visual and gauge checks. Finished parts are inspected and X-rayed to ensure their integrity.
Parts that pass all quality checks are then shipped to our state-of-the-art machining plants equipped with automated German LiCON machining equipment. To ensure precision machining accuracy, clamping is minimized to reduce tolerance errors. Crankshaft PTOs (Power Take-Offs) are custom machined to OEM specifications with intense quality control using manual and laser gauging. Finally, the engine components are dynamically balanced to significantly reduce vibration and improve operator comfort.
PEOPLE
Assembly of Vanguard power solutions is led by Certified Briggs & Stratton Master Service Technicians (MSTs) who have achieved the highest rating in Briggs & Stratton Global Service Training for their craftsman-like approach and attention to detail. They assemble each engine using unique systems and technologies designed to ensure extreme accuracy.
Designed to eliminate human error, “Pick to Light” parts selection uses automated lights to illuminate the proper parts bins for the technician. Block assembly is made more efficient by prearranging engine components into kits that travel through the assembly process until all parts are fitted to the engine. To ensure the accountability construction equipment manufacturers expect, technicians scan their ID badge and the engine serial number as it enters the assembly station. That way each unit contains the digital signatures of all technicians involved in assembly.
The Vanguard Vision System enhances the accuracy of the assembly process. Visual assembly instructions appear on video monitors and direct the technician to the correct component selection and installation. Engines are assembled using DC electric tools. They wirelessly verify and record the torque setting of each critical fastener applied to a Vanguard engine. This automatic control eliminates operator error and ensures accuracy. Finally, before an assembled engine is approved to ship, it is run-tested, speeds are set to the construction equipment manufacturer’s specifications, and all electrical outputs are verified.
PRODUCT
How Vanguard engines are made results in world-class products that are ready to go to work for you right from the plant. Because of the level of reliability and durability they deliver, we back each product with a warranty that is unmatched in the industry.
POWER IN PARTNERSHIP
Learn what it’s like to work with us and why a partnership with Vanguard is just as powerful as our engines. Click the button below to download the article.