Spec’d or Bust: Tips for Choosing a Construction Engine
There’s a lot to consider when spec’ing an engine on construction equipment. What features matter? What is the end-user looking for? Do noise levels make a difference
The right engine can significantly impact the performance of OEM construction equipment. Tom Billigen, training manager, customer education, Briggs & Stratton, answers common questions for ensuring the right engine powers your equipment.

Q. What key engine features are important for the construction market?
A. Construction equipment puts engines through the ringer — dusty, unpredictable job sites and demanding applications all play a factor. That’s why you should spec your equipment with rugged engines that are proven to withstand tough working conditions. Don’t also forget to incorporate productivity enhancing features, such as easy starting and reduced maintenance.
Q. Can engine features help reduce the total cost of ownership of equipment?
A. Yes, actually. Look for engines that specifically incorporate practical innovations — such as reducing fuel consumption without compromising on power. Doing so can give you yet another tool in reducing the overall total cost of ownership.
For example, Vanguard® EFI delivers the power needed for demanding construction applications with its closed loop system. By creating a nearly perfect air-fuel mixture and adjusting the ratio based on load, throttle response and air intake, EFI optimizes fuel efficiency and power. And while fuel savings vary by industry, application and engine family, the 25 percent mark makes the reality of a return on investment (ROI) feasible.
Q. Can an engine improve job site productivity?
A. Absolutely. End-users ultimately want equipment that’s working — not sitting in the shop. That means you should look for engines equipped with features that decrease job site downtime to increase the equipment value.
Here at Vanguard, we surveyed crews to uncover the largest reason for downtime and discovered that oil/fuel dilution during transport was a major factor. In response, we developed TransportGuard® technology, a three-in-one fuel/ignition shut-off that completely eliminates oil/fuel dilution. Other features, such as Vanguard’s cyclonic air filtration, which improves maintenance intervals to 600-hours, can drastically reduce the time equipment spends out of commission for maintenance.
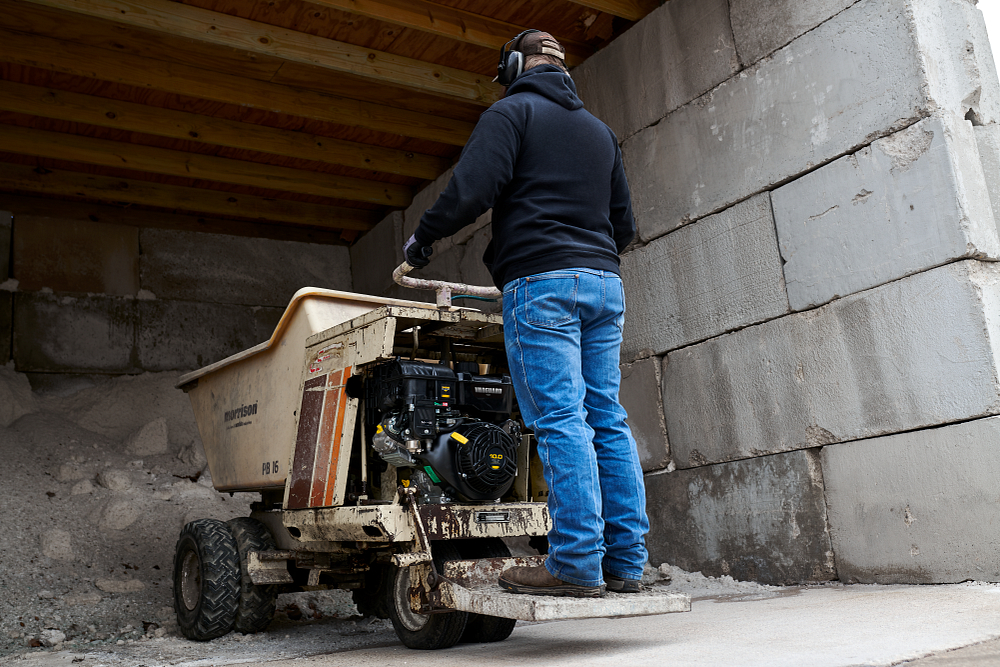
Q. Should the construction industry be concerned with choosing engines that lower noise levels on the jobsite?
A. End-users are often using construction equipment for multiple hours a day for days on end. Spending such a significant amount of time in proximity to that much noise can wear on the operator, thus decreasing productivity. Choosing an engine with both lower noise levels and higher tonal quality can have a significant, positive impact on the user experience.
Not only does it help the operator, but equipment that isn’t overly loud can improve job site safety. For example, if a crew is working on a highway, a loud engine may drown out the sounds of traffic and other equipment — increasing the risk of an accident.
When choosing an engine, it ultimately comes down to reliability, durability and performance. Equipping your products with Vanguard power solutions can help ensure your construction equipment is always ready to take on a challenge and deliver productivity.
MORE INFORMATION
Have more questions? Ask our new tool, Briggs & Stratton Assist for fast and accurate answers.
LOCATE A DEALER
Finding the right dealer is key to getting the right help. Our dealers are certified and specialize in selling or servicing our different product types.